3D Vision-Guided metal parts loading and unloading
Project background: The traditional feeding method often relies on manual operation, which is not only inefficient, but also susceptible to human factors, resulting in unstable product quality. The application of 3D vision technology can realize the accurate identification and positioning of the inertial ring, greatly improve production efficiency and product quality, and reduce production costs and losses.
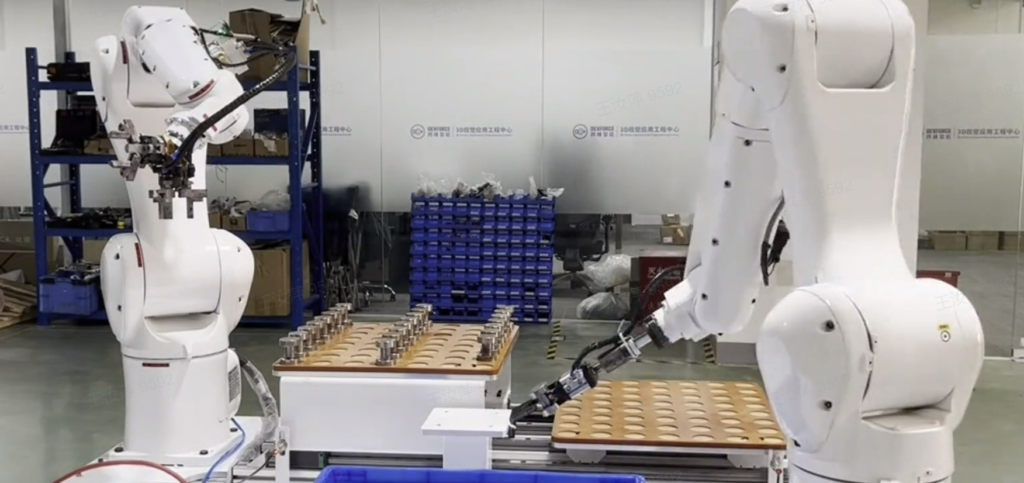
- Project advantages:
- Training deep learning models based on DexForce self-developed DexVerse™ embodies intelligent engine, which can identify various sizes and shapes of workpieces, without repeated model training, and has strong applicability;
- Support to configure multiple product models at the same time, and switch operations according to robot signals; There is no need to stop production to collect annotated data, and the deep learning model training of the new workpiece can be completed in 8 hours, and the production can be quickly launched.
- Zero code, zero programming, direct adjustment of parameters can achieve visual positioning, the fastest 5 minutes to complete visual configuration, 20 minutes to cooperate with the robot to grasp debugging.
- Application results
Based on the DexForce intelligent 3D vision system, it can automatically complete the identification, positioning and processing of metal parts, reducing the frequency and error rate of manual operation. Through algorithm optimization and intelligent control, it can quickly and accurately identify metal parts, realize automatic loading and unloading operation, reduce labor costs and production line maintenance costs, so as to achieve the purpose of cost reduction.